Kraftübertragung auf Rührsysteme – hygienisch abgedichtet
Flüssigkeiten in Reaktoren, Medientanks und anderen Prozessgefässen müssen in der Regel gerührt werden. Dabei stellt sich bei hygienischen Prozessen insbesondere die Frage, wie die Antriebskraft von aussen auf den Rührer im Innern des Behälters übertragen werden soll, ohne dass Flüssigkeit aus dem Kessel austreten kann oder ungewünschte Substanzen – dazu gehören auch Mikroorganismen - in den Behälter gelangen können.
Übertragung der Antriebskraft direkt über eine durch die Kesselwand geführte Welle
Diese Lösung erfordert eine Abdichtung der Welle gegenüber der Kesselwand. Die Dichtung ist in diesem Fall immer dynamisch, und im Dichtelement tritt Reibung auf.
Da einfache Stopfbuchsendichtungen insbesondere aufgrund der großen Porosität alles andere als hygienisch sind, kommt für sterile und hygienische Anwendungen nur die Gleitringdichtung in Frage.
Die Gleitringdichtung ist aus einem stationären, mit der Behälterwand verbundenem Dichtring und einem rotierenden, mit der Welle verbundenem Dichtring aufgebaut. Die Berührungsflächen dieser Ringe sind absolut plan und poliert, dadurch wird eine Passage von Mikroorganismen durch den Dichtspalt vermieden. Mindestens einer der beiden Dichtringe ist aus einem besonders harten Material wie z.B. Siliziumcarbid gefertigt.
Gleitringdichtungen werden meistens mit einer Flüssigkeit überlagert, was die Bildung eines Films zwischen den Gleitflächen der Dichtringe zur Folge hat. Bei einem Untenantrieb kann das direkt die Flüssigkeit im Behälter sein, wie es üblich ist bei Benchtop-Fermentern. Bei einem Obenantrieb, auch bei den kleinen Benchtop-Fermentern, muss dies eine Flüssigkeit außerhalb des Behälters auf der anderen Seite der Dichtung sein. Typischerweise wird Glycerin dafür verwendet.
Bei jeder Gleitringdichtung muss bei drehender Welle systembedingt eine minimale Flüssigkeitsleckage in Kauf genommen werden. Feststoffe und Mikroorganismen können aber eine intakte Gleitringdichtung nicht passieren.
Um die Wahrscheinlichkeit einer Passage von Mikroorganismen und auch den Durchtritt von Flüssigkeit durch die Dichtung im Falle eines Defekts zu reduzieren, wird bei grösseren Fermentern oft eine doppelte Gleitringringdichtung eingesetzt. In diesem Fall wird der Zwischenraum zwischen den beiden Dichtringpaaren mit einer Sperrflüssigkeit überlagert.
Die Sperrflüssigkeit wird über ein Vorlagegefäss dem Zwischenraum zwischen den Dichtungen zugeführt.
In einfachen Fermentern mit unproblematischen Mikroorganismen wird meistens etwa 80 prozentiges Glyzerin als Sperrflüssigkeit verwendet. Diese Flüssigkeit verhindert das Wachstum von unerwünschten Mikroorganismen und verdunstet zudem nur sehr langsam. Eine solche mit Glyzerin überlagerte Gleitringdichtung ist kostengünstig zu realisieren.
Mit größerem technischen Aufwand kann der Zwischenraum aber auch mit sterilem Dampf-Kondensat überlagert werden. Diese Lösung erlaubt auch eine In-situ-Dampfsterilisation des Zwischenraums zwischen den beiden Dichtringpaaren vor oder auch während eines Prozesses. Die Möglichkeit der Dampfsterilisation des Zwischenraums ist üblich, wenn nach GMP-Empfehlungen gearbeitet werden muss und insbesondere auch, wenn pathogene Organismen kultiviert werden.
Eine direkt durchgeführte Welle erlaubt die Übertragung maximaler Drehmomente. Das System eignet sich daher besonders gut für mikrobielle Kultivierungen, die einen hohen Sauerstoffbedarf haben und daher auch hohe Rührerleistungen benötigen.
Außerdem kann ein Antrieb mit Gleitringdichtung problemlos gereinigt werden.
Übertragung der Antriebskraft über ein Magnetfeld ohne durchgehende Welle
Bei dieser Lösung wird keine Welle durch die Kesselwand geführt. Die Welle mit den darauf montierten Rührorganen befindet sich vollständig innerhalb des Behälters, eine dynamische Dichtung ist nicht notwendig. Die Welle muss aber vollständig innerhalb des Kessels gelagert werden.
Die Kraft des Antriebmotors wird nicht direkt über mechanische Elemente, sondern nur über ein Magnetfeld durch die Kesselwand auf die Welle im Kessel übertragen.
Eine Leckage ist unmöglich, solange allfällig vorhandene statische Dichtungselemente, z.B. O-Ringe, unbeschädigt sind.
Da sich diese Wellenlagerung, oft sind es auch zwei oder sogar drei Lagerungen pro Welle, innerhalb des Kessel befindet, liegen zwangsläufig mehr oder weniger grosse Toträume innerhalb der Prozessflüssigkeit, z.B. die Spalten zwischen den Lagerbuchsen oder zwischen einer allfälligen Führungswelle und der eigentlichen, rotierenden Welle. Diese Zonen können nur mit erheblichem konstruktiven Aufwand so gestaltet werden, dass eine zufriedenstellende Reinigung gewährleistet werden kann. Die Magnetantriebe von Bioengineering sind bezüglich guter Reinigungsfähigkeit optimiert.
Ein Magnetantrieb erlaubt nur die Übertragung begrenzter Drehmomente. Sehr hohe Rührerleistungen können mit diesem System nicht in den Behälter eingebracht werden. Deshalb kommen Magnetantriebe eher bei Zellkulturen zum Einsatz, bei denen typischerweise nur tiefe Drehzahlen zur Anwendung kommen.
Übertragung der Antriebskraft direkt über nicht rotierende mechanische Bauteile
Selten nachgefragt und eingesetzt werden auch Rührerlösungen, bei denen die Antriebskraft direkt über ein nicht drehendes mechanisches Bauteil, meistens ein Stab, durch die Kesselwand auf das Rührelement übertragen wird.
Anstelle einer Rotationsbewegung wird eine oszillierende vertikale Bewegung erzeugt oder eine Pendelbewegung, idealerweise zu einer Lemniskaten-förmigen Bewegung erweitert.
Typische Vertreter des Antriebstyps mit vertikaler Oszillationsbewegung sind Vibrationsmischer. Systeme mit Pendelbewegung sind nicht als standardisierte Lösung verfügbar.
Beide Systeme erfordern keine dynamische Dichtung; eine Leckage ist nur möglich, wenn die statischen Dichtungselemente versagen. Die Dichtungselemente bestehen aus elastischen Membranen oder Faltenbälgen aus Metall oder Kunststoff. Konstruktiv bedingte Toträume, die eine Reinigung erschweren, können so vermieden werden.
Allerdings sind grosse Antriebsleistungen nur mit viel technischem Aufwand, wenn überhaupt, in den Prozess übertragbar. Auch werden solche Systeme nicht als Untenantrieb realisiert und sind entsprechend weniger bedienungs- und servicefreundlich: auch bei kleineren Kesseln ist eine Hebeeinrichtung notwendig, um den Kessel für Reinigung oder Service zu öffnen. Zudem beansprucht ein Obenantrieb viel Platz im Deckelbereich, der dann nicht mehr für Messtechnik oder Zudosiereinrichtungen zur Verfügung steht.
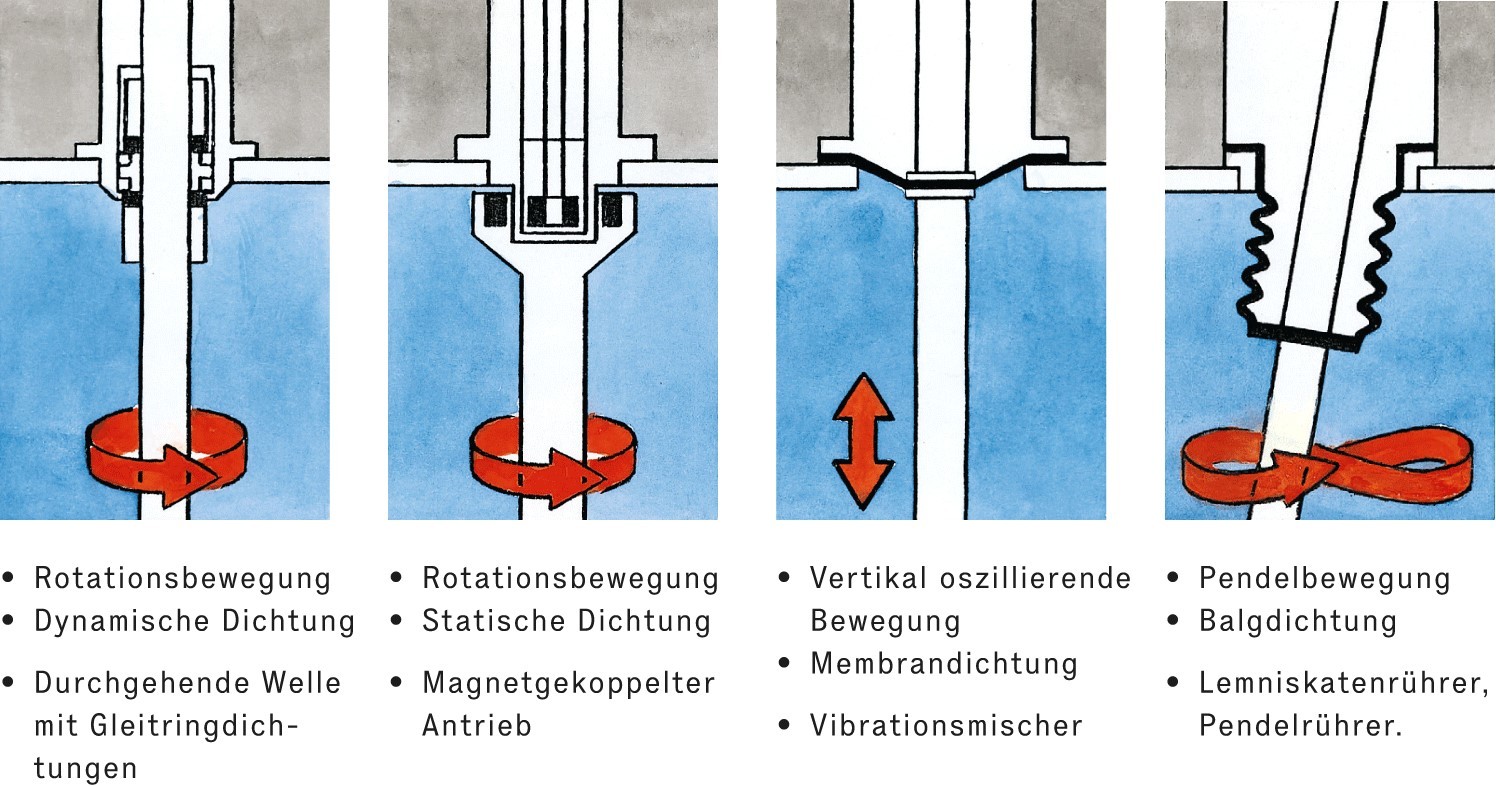
Bioengineering bietet grundsätzlich alle Lösungen an. Rotierende Antriebssysteme mit Gleitringdichtung werden am häufigsten eingesetzt, gefolgt von magnetgekoppelten Systemen.
Gerne berät Bioengineering AG die Anwender bei der Wahl des am besten geeigneten Systems.